|
October 20,
2004 |
Compact Size and High-Precision Operation from Newly Developed
Vertical Scroll Milling Machine
- Three New Models to be Exhibited at the 22nd Japan
International Machine Tool Fair -
Toyo Advanced Technologies Co., Ltd. announced the development of
the T-400SCV, a vertical scroll milling machine for producing disc-shaped
parts with fins in a coiled configuration (such as scroll-type compressors
for air conditioners) with a high degree of precision. The T-400SCV
is scheduled to go on sale in February 2005.
The new scroll milling machine is compact, measuring only 1 meter
wide, but provides excellent performance. It mills scroll fins with
a profile precision of ±5μm. Furthermore, its environmentally friendly
design reduces power consumption by 50% and air consumption by 65%
compared with conventional horizontal scroll milling machines.
Toyo Advanced Technologies will be exhibiting the T-400SCV at the
22nd Japan International Machine Tool Fair, to be held from November
1 to 8 at Tokyo Big Sight. Other new products on display will include
the T-11JA CNC internal grinding machine, scheduled to go on sale
in November, and the T-11LA88 internal grinding
machine, which is capable of grinding two bearing interiors simultaneously.
The exhibit will also feature units demonstrating Toyo's high level
of technical achievement, including airless milling heads with superior
rigidity and highly rigid high-output wheel heads.
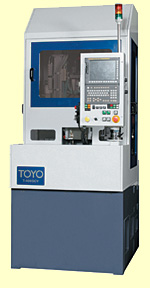
|
|
T-400SCV Vertical Scroll Milling Machine |
Products to be Exhibited at the 22nd Japan International Machine
Tool Fair
Machines |
T-400SCV Vertical Scroll Milling Machine |
T-11JA CNC Internal Grinding Machine |
T-11LA88 CNC Internal
Grinding Machine (Grinds 2 Pieces of Work Simultaneously) |
Units |
HAB01 Series Highly Rigid Airless Milling
Heads |
HFD Series Highly Rigid High-Output Wheel
Heads |
Overview of Machines to be Exhibited
T-400SCV Vertical Scroll Milling Machine
More than 150 Toyo horizontal scroll milling machine have been
sold since the first models went on the market in 1990, positioning
them among our best-selling products. The newly developed T-400SCV
has a vertical orientation that makes possible a compact footprint.
It is equipped with a custom dual-head spindle and a high-output servo
motor for high-speed, high-precision milling performance.
The T-400SCV is designed for the production of scroll-type compressors
of the type used in room air conditioners, automobile air conditioners,
and hot-water heaters. Such compressors are becoming more compact,
and the T-400SCV is able to accommodate work sizes down to a minimum
diameter of only 20 mm. The maximum work diameter is 80 mm, and this
can optionally be extended to 120 mm. With the addition of the T-400SCV
to the two horizontal models now available, Toyo will offer a lineup
of three scroll milling machines. The T-400SCV is presently being
used as the basis for development work on a new vertical internal
grinding machine.
* |
Compact footprint: At 980 mm, the T-400SCV is less than 1
meter wide. Its footprint is 80% smaller than that of conventional
horizontal scroll milling machine. |
* |
High-speed, high-precision milling: The T-400SCV delivers
profile precision of ±5μm, a level difficult to attain with
a machining center, through the use of constant milling point
control (which increases profile precision by controlling movement
in the direction of machining error caused by head deformation
due to heat). This technology has received a very favorable
response in our horizontal scroll milling machines. Furthermore,
the dn value 2,000,000/40,000 rpm and dn value 1,800,000/45,000
rpm dual-head spindle, weight reduction, and a high-output servo
motor provides high tracking accuracy, contributing to high-speed,
high-precision milling performance. |
* |
Energy efficient: Air consumption has been reduced 65% by
switching from a conventional oil-mist system to an oil-air
system as the spindle lubrication method. Components such as
the spindle amplifier and servo motor have been optimized to
reduce power consumption by 50%. |
* |
Easy setup and loading: The C-axis moves automatically to
the loading position (the work side at the front of the machine)
to facilitate setup and loading. |
T-11JA CNC Internal Grinding Machine
The T-11JA, a high-performance general purpose internal grinding machine
suitable for a wide range of applications, was announced in September
and will go on sale in November. It has already been exhibited in
the United States, at the International Manufacturing Technology Show
in Chicago in September, but this marks its first appearance at the
Japan International Machine Tool Fair. Many customers have already
expressed interest, and it looks like the T-11JA will sell well.
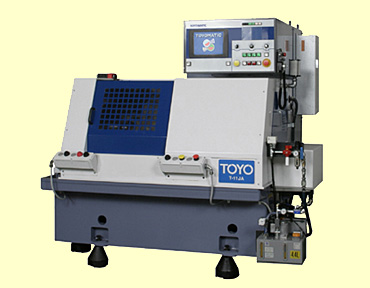 |
T-11JA CNC Internal Grinding Machine |
The main features of the T-11JA are as follows.
* |
Supports many types of grinding, including multi-face continuous
grinding of up to eight faces, taper grinding, and internal-R
grinding. |
* |
In addition to the teaching function, the T-11JA can store
39 grinding conditions in its memory. This simplifies preparation
and setup for repetitive production tasks. |
* |
The T-11JA can accommodate work diameters ranging from Φ1.5
mm to Φ170 mm, making it suitable for a wide variety of applications. |
* |
While providing the convenience of automated operation, the
T-11JA delivers the feel of manual grinding. |
* |
The T-11JA is ideal for small-volume production of a wide
variety of work, including automobile parts, dies, and general
machinery parts. |
T-11LA88 CNC Internal Grinding Machine
The T-11LA88 is a centerless model in Toyo's
acclaimed T-11L series of internal grinding machines. The configuration
to be displayed at the show, which can grind two pieces of work simultaneously,
is based on the T-11LA88 internal grinding machine.
It reduces space requirements, saves energy, reduces costs, and achieves
high efficiency by grinding the interiors of two bearings at once.
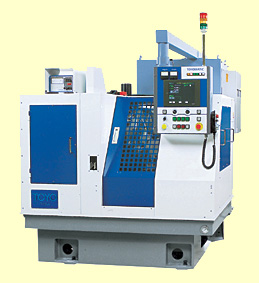
T-11LA88 CNC Internal Grinding Machine |
* |
Separate pairs of in and out shoots and a special device for
synchronizing two flows of bearings allow stable and simultaneous
loading of two pieces of work. |
* |
Two bearing grooves (outer surface of inner ring), or two
sets of inner surface of inner ring, can be grinded simultaneously.
This makes it easy to double production output. |
* |
Grinding two pieces at work at the same time cuts running
costs in half. |
|
|